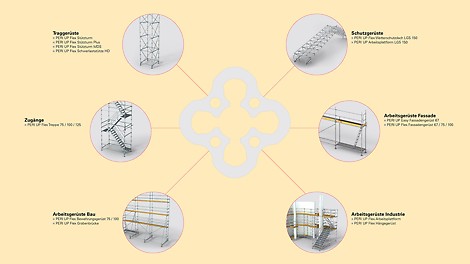
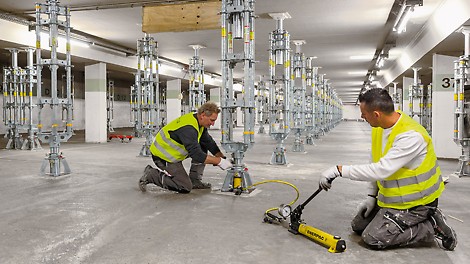
Download Press Release
The images in more detail
In the 1960s, the first closed frame scaffolds appeared on the market while the first modular scaffolding followed around a decade later. Since then, contractors have been faced with ever-increasing cost pressures and stricter safety regulations. Frequently, manufacturers have developed new, complementary system components so that the range of components within the individual scaffolding systems in particular has likewise steadily increased. This has resulted in disadvantages such as a rise in storage and logistics expenditure as well as increased planning and assembly costs.
PERI has followed a completely different strategy and logic: based on decades of experience in formwork and shoring technology, the Weissenhorn-based company developed a new type of scaffolding system in the late 1990s. The focus of the development was placed on avoiding additional safety measures in particular and integrating assembly safety into the system by means of constructive measures. Thus, the PERI UP T 72 / T 104 Frame Scaffold featuring the guardrail in advance was created. This was followed ten years later by the development of a modular scaffold system complete with metric grid dimensions, which is characterized by a high level of safety and flexibility. With the aim of combining the advantages of both variants to create an extremely versatile system with a minimum number of different system components, this led to PERI launching the innovative PERI UP Easy Frame Scaffold in 2016. This latest development in the PERI UP scaffolding technology is now setting new standards in terms of innovation.
The development goal: uncompromising efficiency and safety
The team of developers faced the challenging task of aligning the scaffolding system in terms of length, height and width to conform to metric dimensions and to use as few system components and connecting elements as possible. The fact that the scaffold system had to provide a high degree of safety was beyond all question. Furthermore, the focus was on ensuring a high level of efficiency so that users can meet the ever-increasing demands of the market accordingly.
The result: reduced to a maximum
As few components as possible together with the highest possible utilization rate – this was achieved through the consistent use of the PERI rosette node. The modular scaffolding had already used this node as a central connection element for connecting up to eight different components. Now the frame design of the new PERI UP Easy Facade Scaffolding also takes advantage of this versatile node connection: each Easy frame features a ¾ rosette node which is used to connect the components of the modular version. In order that all components of both variants can be seamlessly combined, the modular scaffolding standards and the frames of the frame scaffolding have been designed with identical height dimensions. As a result, PERI UP components can be flexibly combined with each other on a horizontal level so that stairs, among other things, can be easily connected to the frame scaffolding. The resulting PERI UP Modular Scaffolding Kit facilitates all typical applications in scaffolding operations and also ensures that complex solutions are extremely cost-effective.
Regardless of whether it is shoring, facade, safety or working scaffold – PERI UP now covers the common application areas of scaffolding technology with one single system. As a result, PERI UP offers the possibility of being able to respond quickly to changes in the construction process without having to resort to provisional solutions, which is very often the case.
Large range of applications with only 500 components
From 3D scaffolding in building construction and reinforcement scaffolding in concrete construction through to heavy-duty props for civil engineering – PERI UP has a particularly broad range of applications with regard to the small number of components available. This has several advantages for the user: more cost-effective utilization of the individual system components, less storage and transport areas as well as lower costs for maintenance and repairs.
Likewise, the small number of individual components has a positive effect in connection with assembly operations as the assembly team can also save time due to having fewer different components and connections. The simple manageability of the scaffolding during day-to-day work on the jobsite additionally motivates the users. In the end, the effect of the increase in work productivity reaches the client and leads to higher customer satisfaction.
Safety and flexibility is what counts
The design of the guardrail in advance for the PERI UP Easy Facade Scaffold is an example of the fact that user safety while ensuring cost-effectiveness needs not be a contradiction. After all, if safety technology is integrated in the system and the design only allows safe assembly, this leads to increased work performance. The solutions used by PERI UP deliberately do without any subsequent installation of additional components and thus define the current state of technology.
In addition to the speed of assembly on the facade, the adaptability to match the contours and geometries of the respective structure is a decisive criterion for the cost-effectiveness. Projections and recesses in the facade as well as cantilevered or freestanding components – all of this can be accomplished equally well thanks to the unique combination possibilities of the PERI UP Frame and Modular Scaffolding.
Scaffold operations in a new dimension
PERI UP removes the system boundaries between frame and modular scaffolding and meets all challenges faced in the markets. Due to the flexible utilization and the sophisticated solutions, all requirements regarding safety, load-bearing capacity, time expenditure and customer benefits can be met with just one system.
In addition to system-related assembly and safety advantages of PERI UP, competent and on-going project support is an important factor in reducing time and costs. Thus, PERI engineers support the execution from the first planning idea through to the last return delivery. Among other things, the detailed 3D scaffold planning along with early coordination with all parties involved increase work safety and efficiency.