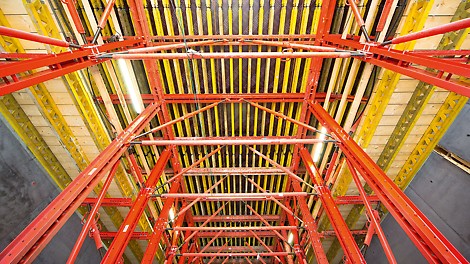
Download Press Release
The images in more detail
The "Nordhavnsvej – Vej- og Tunnelentreprise" project is the largest infrastructure project in Copenhagen of the past 50 year. The 1.65 km long route will eventually link Copenhagen´s northern port area with the Helsingør motorway. It runs through a very densely built urban area including depths of up to 22 m. One particular challenge regarding the execution was planning the course of the tunnel because the underground structure also crosses a very busy railway line. Completion of the complex connection of road and tunnel has been scheduled for autumn 2015.
The formwork solution for the tunnel
For the realization of the two tunnel tubes – each with 2 lanes – PERI planned a solution with wall formwork in advance and one slab formwork carriage which subsequently followed; this has been implemented in accordance with the requirements of the two joint venture partners.
The high demands placed on the design and concrete surfaces in the tunnel entrances have been fulfilled with a project-specific Vario GT 24 girder wall formwork solution. For the formwork elements of up to 12.80 m high and almost 25 m long, the construction team is using load-bearing, durable formwork girders of specially produced lengths.
The bottom slab and all other tunnel walls are concreted using the proven Trio panel formwork, in part single-sided against the bore pile wall of the sheet piling. The individual elements of the tried-and-tested formwork system are connected to form large-sized units which can then be moved extremely quickly by crane to the following casting segment.
For the subsequent construction of the 80 cm thick slabs, PERI engineers planned a total of 4 identical slab formwork carriages, each 13.50 m long, on the basis of the Variokit engineering construction kit. Two formwork carriages are coupled one behind the other per tube in order to concrete the 25 m long slab sections in each case. The highest priority for the design of the tunnel formwork carriage was to ensure simple and fast operations. For lifting and lowering, a hydraulic solution is therefore used so that adjustments can be made to the carriage in only one day for the next concreting section. The construction is then pulled to the following segment on crane rails by means of flanged wheels.
By bracing the formwork carriage using SLS heavy-duty spindles, a 4.00 m high and almost 4.30 wide access passage for site traffic could be realized. This was requested by the client so that the required materials can be delivered unimpeded. In order to construct the haunch on the support to the middle wall, a section of the slab formwork can be folded down by means of a spindle. To operate these spindles, the formwork carriage is equipped with cantilevered working platforms.
Thanks to the simple solution for the slab formwork carriage, the construction crew quickly became familiar with the operating procedure. The fact that well over 90 % of the carriage components are rentable system components also makes the solution extremely cost-effective. Special components are required in only a few sections – among other things for the stopend formwork. This is comprised of two formwork units arranged on top of each other which means that the required water stops between the concreting sections are easy to install and securely fixed in the correct position.
Access points and working scaffold – everything from one source
The stairways needed for the working areas and work scaffold are also supplied by Peri. As access to the slab formwork, the Alu 75 site staircase is used which is assembled with system components of the Peri Up Rosett Flex modular scaffolding. For the Copenhagen project, the 4-legged tower with staircase units in the same direction is mounted on the slab formwork carriage and the two are moved together to the next section each time.
The reinforcement scaffold is also assembled using system components of the modular scaffold. The scaffold units each consist of 3 bays with a length of 250 cm, and can be quickly moved to the next place of use using transportation wheels. This not only saves crane time but is also the only possible solution in those areas where the tunnel structure crosses the railway line. For fast and safe working operations, the scaffold – complete with integrated stair access and cantilevered brackets – is optimally adapted to match the available working area as well as the course of the concrete wall.
With an integrated system grid of 25 cm and 50 cm, the Peri Up Rosett Flex is extremely flexible; with the "gravity lock" and self-securing decks, every construction can be quickly assembled. A high level of safety is provided by the end-to-end guardrails and gap-free toe boards in a bright signal colour. The perforated surface of the decking also guarantees high slip resistance.
The "Nordhavnsvej – Vej- og Tunnelentreprise” project
The connection of the northern port area with the motorway through the densely built downtown district of Copenhagen is currently one of the largest construction projects in the city. The Nordhavnsvej – a combination of tunnel and an above-ground roadway – is scheduled for completion after a 4-years construction period with a total cost in the region of 2 billion Danish Kroner.
The road is designed to improve the connection to the port as well as ensuring that traffic noise levels for the residents of Copenhagen and the neighbouring town of Gentofte is greatly reduced. After the official opening in 2015, it is expected that around 15,000 cars will use the new connection per day.