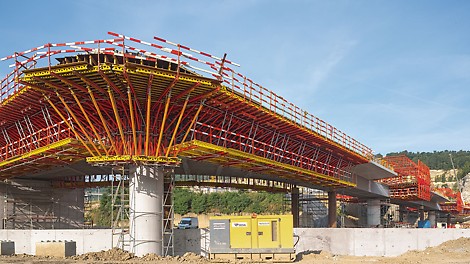
Download Press Release
The images in more detail
The Lanaye locks are located on the border between Belgium and the Netherlands and combine the Albert Canal with Juliana Canal, a side canal of the River Meuse. Through the construction of additional lock chambers, the capacity will therefore be quadrupled. Integral part of the complex building project is the new 200 m long road bridge which crosses the shipping channel at right angles.
The S-shaped, 15 m wide bridge is a steel composite construction and has unusually large cantilever lengths of 4.50 m. For their realization, formwork solutions on the basis of the Variokit engineering construction kit from Peri were selected: the 136 m long main crossing is being completed with the help of two Variokit composite formwork carriages whilst the Peri bridge solution featured radially-arranged Variokit cantilever brackets for realizing the two almost 30 m long extremely tight curve radii.
Steel composite carriages
The steel composite construction method is based on the interaction between steel beams and reinforced concrete. In the first step, a steel beam in the form of a hollow box cross-section was positioned, after which the reinforced concrete slab was formed by means of two independently-operating Variokit formwork carriages. Thus, a total of 13 casting segments with lengths ranging from 8 m to 12 m could be constructed whilst maintaining the required striking times in what was a very tight schedule.
The composite formwork carriages are moved on heavy-duty rollers which are mounted on supports on the steel construction with 4 m spacings. Their construction is based on a longitudinal truss consisting of standardized main beams which have been modularly adapted to match the geometric and static boundary conditions. In addition, the lateral units of the Variokit system could be flexibly adapted to suit the specified bridge section – this has led to extremely economical project solutions. Furthermore, the on-site application has resulted in efficient and safe working operations: thus, for example, the tie suspensions of the cantilever formwork can be operated entirely from above.
Cantilever brackets
On both banks of the river, the bridge construction features two 90° bends – complete with extremely tight axis radii of almost 30 m respectively. For this, Variokit cantilever bracket units mounted on steel beams have provided an ideal construction site solution.
In addition, the complex geometric and static area where the circular columns are positioned have been shuttered using Peri know-how and, for the most part, with standard materials. Here, the external brackets are arranged radially with the pressure support on the available reinforced concrete columns by means of Variokit components and Multiprop 625 aluminum slab props playing an important part in the Peri project solution.
Teamwork-oriented complete solution
For ensuring rapid final assembly and problem-free construction site use, formwork units were delivered already pre-assembled. Here, Peri formwork assembly teams in German Weissenhorn and Düsseldorf provided dimensionally-accurate fabrication and punctual delivery. In order to achieve the best possible construction results, the technical processing and static calculations were carried out from the beginning onwards by Belgian and German Peri engineers in exemplary international teamwork.
Already during the construction of the bridge piers as well as lock components, the system solutions ensured that work operations could be performed efficiently and cost-effectively. Thus, one set of climbing formwork complete with GRV articulated waler formwork served to form the circular reinforced concrete piers featured in the ground plan. Due to the system-related closed ring tension, the 2.50 m diameter piers were thus realized without any anchor points.