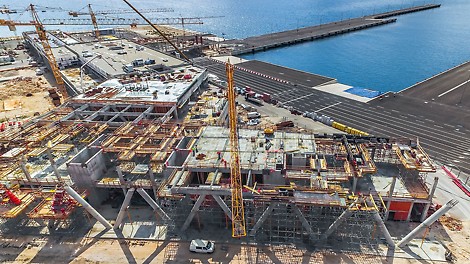
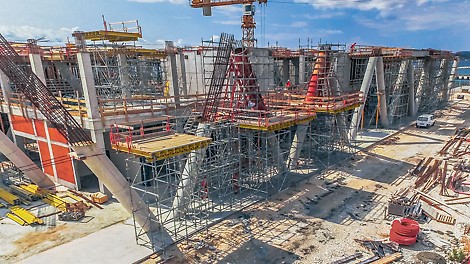
Download Press Release
The images in more detail
The ferry port in Gazenica is only 3 km from the centre of the Croatian town of Zadar. The new landing facility will relieve the historic harbour in the old town which is a designated UNESCO World Heritage Site. Due to the larger capacity provided by the jetties for ferries and international ships, the new passenger port on the Adriatic coast will also be a new destination for large cruise ships in this attractive tourist region. After completion, ships with a length of more than 400 m can also dock in this modern port. As part of the extensive construction measures, a two-story passenger and ferry terminal has been realized on a total area of 25,000 m².
V-shaped inclined circular columns in the best architectural concrete quality
The most striking and technically challenging design element of the terminal skeleton construction has been the 10.30 m high circular columns – forming a V-shape due to being inclined at the angle to each other – that characterize the entrance areas of the terminal building.
For the realization of the 60-degree inclined circular columns, customized PERI SRS Circular Column Formwork was used. Due to the high manufacturing quality of the steel formwork, columns with diameters of 95 cm and 100 cm could be produced with the best surface quality. In order to support the first – 6 m high – concreting section, SRU Steel Walers and Heavy-Duty Spindles taken from the VARIOKIT Engineering Construction Kit were used. For concreting the second section, the construction team installed a working platform supported by PERI UP Flex Shoring that, thanks to the 25 cm system grid of the modular scaffolding, could be flexibly adapted to accommodate the circular columns which are diagonally-positioned across the inside of the structure. PERI UP Flex Stairs served as a safe and secure access solution.
The square-shaped columns of the skeleton construction were concreted using PERI TRIO Column Formwork. Due to the high fresh concrete pressure that could be accommodated by the formwork, the 5.50 m high columns could be realized in one pour. The TRIO Formwork System facilitated fast assembly as well as allowing the formwork to be easily moved from column to column.
DUO and TRIO – an unbeatable team
The foundations and side walls of the beams were formed with the universal DUO System Formwork. Through its low weight and particularly easy handling, the construction team could quickly carry out assembly, forming and moving operations, and without the need of a crane. If required, the entire formlining could be easily replaced without the use of any special tools.
Because of its numerous advantages, the construction team formed the reinforced concrete core walls with TRIO Panel Formwork. A clear plus point of the TRIO Formwork System was, among other things, the possibility of moving large-sized units by crane which in turn saved valuable working time. The minimum number of different components along with the universally usable BFD Alignment Coupler made forming with the proven panel formwork easy and fast.
Slabs systematically formed – also with large supporting heights
For forming the reinforced concrete slabs of the atrium, MULTIFLEX Girder Slab Formwork was combined with the PERI UP Flex shoring system due to the large supporting heights and the specific building design. The free arrangement of GT 24 and VT 20 Formwork Girders allowed the slab formwork to be flexibly adapted to suit the different ground plans. For accommodating the heavy loads and large spans, the particularly strong GT 24 Lattice Girder was used as twin main beams. Furthermore, the flexible PERI UP shoring system could also be adapted in the ground plan to suit the different geometries and load situations – from shoring towers with dimensions of 25 cm x 25 cm through to 4 m x 4 m birdcage scaffolding.
The SKYDECK Panel Slab Formwork made it possible to quickly form the slabs in the areas between the beams. In addition to the simple and systematic assembly sequence, the system was particularly convincing through the possibility of early striking. The panels and main beams were very quickly available again for subsequent concreting sections by means of the drophead – only props with dropheads and cover strips remained in position in order to support the construction. This saved valuable time and reduced on-site material requirements.