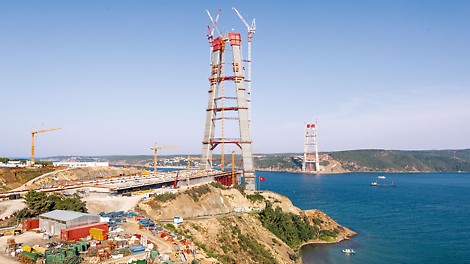
Download Press Release
The images in more detail
The 59 m wide bridge carries 8 lanes and 2 railway tracks with a span of 1,408 m across the Bosphorus, and connects – as part of the new 260 km long North Marmara Motorway – the European and Asian continents. Thanks to the PERI ACS self-climbing system and VARIO GT 24 girder wall formwork, the high requirements in terms of flexibility, surface quality and dimensional accuracy have been met. The efficient workflow processes from one level to the next has resulted in very high productivity and extremely short cycle times made possible through the hydraulic climbing system.
ACS self-climbing system, optimally adapted to the complex geometries
For the inclined surfaces of the A-shaped pylon legs, the adjustable version of the ACS V self-climbing formwork is being used. This can be optimally adapted to suit the sloping side surfaces of the pylons. In order to facilitate safe and ergonomic working conditions at great heights also on inclined structures, the working platform is always positioned horizontally. For the almost vertical surfaces, forming is carried out using the ACS R version which is the standard system of the ACS self-climbing formwork. Within the pylon legs themselves, the ACS P platform version is being used alongside the ACS V.
A major challenge during the planning phase was to adapt the formwork solution in order to match the cross-section requirements of the four pylon legs which steadily become narrower as they climb upwards. The construction has a triangular-shaped base structure with broken corners. Over the height of the pylon, the three long polygon sides are reduced by 1.40 m respectively. The required adjustment of the working platforms has taken place by means of centrally positioned filler platforms whose supporting surfaces are easily adapted to the outer neighbouring platforms. The formwork adjustments are realised using compensation plates and bolted filler elements which are gradually dismantled accordingly.
In addition, the PERI self-climbing solution provides, in particular, the flexibility needed when assembling the steel mounting parts for the stay cable holding devices. The planning solution takes into consideration the varying dimensions and positions of the large-sized steel mounting components. Determining the climbing axes required a well thought-out planning process in order to avoid any collisions with the stay cable boxes. For this, a high degree of dimensional accuracy is required.
Complete solution from PERI – high degree of workplace safety, enhanced efficiency
All ACS climbing units are provided with a trapezoidal sheet cladding. The enclosure of the lower working platforms with completely closed trapezoid sheeting provides anti-fall protection as well as additional wind and weather protection for site personnel. From the other working platforms on Level +1 and Level +2, the reinforcement in advance is installed for the entire next floor. The perforated trapezoidal metal sheeting in this area lets through light and air. Up to 42 tons of reinforcement materials in total can be stored on the top three platform levels.
On the forward-inclined platform, a rotary distributor for concreting is climbed at the same time. Access to the elevator was also integrated in the self-climbing system during the planning phase. This well thought-through solution, along with the creation of 3D views for visualization, was implemented within a short time by all site personnel in efficient teamwork operations. The experience and competent planning, as well as just-in-time deliveries of large amounts of material from PERI, have facilitated problem-free working and thus maintaining the short construction schedule.
Relieving the infrastructure bottlenecks in Istanbul
The megacity of Istanbul, with around 15 million inhabitants, is the fourth largest city in the world. It straddles two continents and two seas and makes the Turkish metropolis unique but, at the same time, it is plagued by chronic traffic problems. In particular, the two existing Bosphorus crossings from 1973 and 1988 are tremendously overloaded. The new North Marmara route bypasses the centre of Istanbul by a wide margin, crossing the Bosphorus about 25 km to the north of the city centre. The third bridge at the outlet to the Black Sea – also known as Yavuz-Sultan-Selim Bridge – is not only the bridge with the highest concrete bridge piers but also the largest concrete suspension bridge with railway tracks in the world. As a direct connection to the planned mega-airport, it should relieve the two existing bridges quite considerably. The completion of this ambitious project is planned for 2015.